How to Perform Lift Station Maintenance
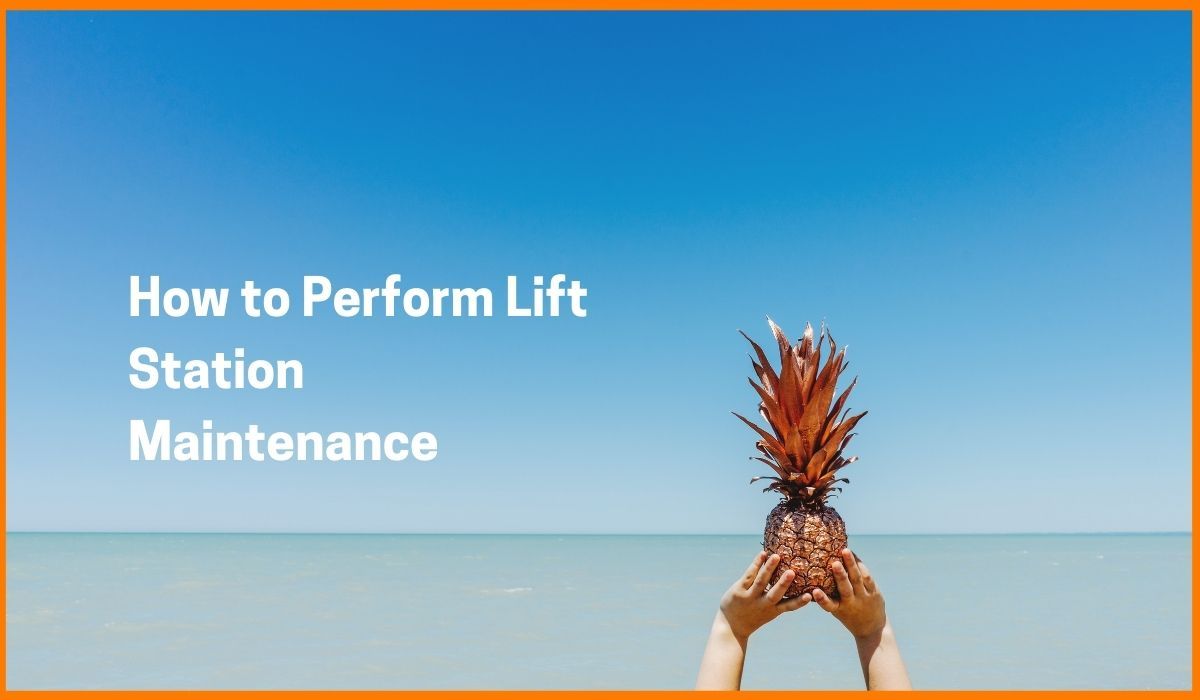
A lift station is available in offices when the gravity stream is not ideal because of elevations or limitations. Lift station systems can be used in both clean and stormwater applications. Likewise, these stations are alluded to as dock siphons, sump siphons, sewage ejectors, siphon stations, or lift siphons. Hence, they require standard inspection and upkeep to continue legitimate execution regardless of the tremendous burdens it encounters.
Lift stations can have a great life span as a useful resource. Steel lift siphoning stations typically have a useful life of 15-20 years, or conceivably more with proactive maintenance. The lift station’s average lifespan can be credited to the continuous fixes’ nature over the long haul. It is accordingly essential to perform legitimate maintenance on lift stations. Cloud-based SCADA software can be exceptionally valuable since they give an automated technique to guaranteeing your lift station’s superior functionality paying little heed to its age.
What is a Lift Station?
A wastewater lift station is a siphon station intended to move wastewater, or sewage, from a lower to higher rise utilizing an assortment framework. These siphon stations are frequently used to move wastewater from private and business offices to their last objective: wastewater treatment plants. Read more about Samsara's guide on lift stations to know more.
When to Do a Maintenance
Maintaining a lift station can be daily, weekly, monthly, quarterly, or annually. With SCADA software, administrators do not always have to visit on-site. Likewise, they can organize their most significant work from anyplace while maintaining the system. If companies plan to do it daily or weekly, they should:
- Examine the lift station visually or audibly.
- Record siphon hours for each siphon.
- Check for lopsided siphon run times.
- Wash down the wet well.
- Check for sand and slop aggregation.
- Check for signs of high water levels.
- Inspect lights and alert frameworks.
Monthly, they should:
- Investigate each siphon for appropriate siphoning (run each siphon through manual control, watch level ascent, and fall).
- Pump down wet well to the absolute bottom, and make a visual investigation.
- Check wet well floats.
- Exercise suctions and release valves.
- Test back-up generator for unwavering quality.
Quarterly, it is best for companies to:
- Eliminate excessive coarseness and oil with VAC trucks.
- Test generators, under load, for 15 minutes.
- Inspect siphons by checking it and channeling for defects, recording amperage readings for each.
- Clean and assess floats.
If a company plans to do maintenance annually, it must:
- Examine electrical hardware such as consumed wiring, connections, parts, corrosion, or dampness.
- Pump and clean wet wells
- Clean submersible level sensors, if relevant, by utilizing a mild cleanser.
- Inspect and clean check valves.
- Pull siphons and perform siphon examination.
Aspects to Be Evaluated
Water companies utilize SCADA software to distantly screen and control siphons, engines, water tanks, and other essential equipment. Experiences from the software help relieve resource failure and guarantee water services are continually running efficiently. In lift station maintenance, these aspects should be exhaustively assessed by companies:
- Voltage
- Amperage
- Outside siphons
- Siphon Functionality
- Wet well condition
- Discharge channeling
- In-line check valves
- Water level sensors
- Siphon regulators
- Telemetry system
- Emergency reinforcement gadgets
- Generator functionality
- In-line processors related with a clean waste stream
While these aspects require rigorous inspection, there is an easier way to check these aspects. Clients of cloud-based wastewater solutions approach their information from any versatile internet browser or cell phone. SCADA software encourages users to limit human on-location visits to the lift station for hardware assessment. It additionally guarantees that administrators can depend on secure and continuous admittance to their information wherever that versatile remote access permits. As a SCADA solution provider, Samsara provides a limitless number of credentialed clients to safely get to the controls and information from any internet browser or cell phone. There is no restriction to the entrance given by the stage that could upset permeability.
Operational Strategy: Run to Fail
“Run to fail” suggests that the association will expect unavoidable disappointments and have adequate extra parts and staff close by to keep the vacation beneath hierarchical prerequisites. The reasonable personal time is typically determined on a station-by-station premise.
Rush to fail is a maintenance procedure where support is possibly performed when equipment has fizzled. In contrast to impromptu and responsive maintenance, appropriate run to fail support is an intentional and considered technique intended to limit total support costs. By and large, it is an incredible upkeep system; however, it is horrible for others.
Option 1: Preventive Maintenance
More normal among medium-sized and more prominent companies was a degree of preventive maintenance, e.g., adjusting the impellers and seals inside a set period or measure of run time, such as regular intervals, like clockwork, so forth.
Companies with preventive support methods accepted that running to fail was imperfect, and there was an "obligation of care" duty to keep the resources in a decent condition. Most utilities with this strategy recognized that they did not know whether they were doing a lot of support. In any case, by and large, they were alright with their degree of expenditure and were not encountering an elevated level of disappointments. Additionally, their solace with their degree of the cost was usually because they had gotten familiar with it.
Option 2: Predictive Maintenance
Predictive maintenance depends on the standard of checking the exhibition of the machines while they are working. Performance observation expects to assess both when machines can break down and the reason behind. This maintenance innovation depends on how machine parts give particular kinds of caution before they break down. The vibration was utilized as the failure identification boundary, as it provides an admonition of practically all typical failures, found in siphons and electrical engines, heretofore.
Conclusion
While lift stations inside a wastewater treatment infrastructure give intrinsic benefits over the significant expenses of underground gravity sewer frameworks, actually assessing these lift station resources can be time and labor-intensive. By utilizing SCADA software and far off checking systems, there are more opportunities to diminish operating expenses productively.
Must have tools for startups - Recommended by StartupTalky
- Convert Visitors into Leads- SeizeLead
- Manage your business smoothly- Google Workspace
- International Money transfer- XE Money Transfer